Spray bars for the food industry
Get in touch with questions about spray bars or start your specification HERE.
Spray bars are used extensively in the food manufacturing and processing industry. They enable the positioning of nozzles along an axis, increasing the coverage area of the spray. SNP offers easy-to-configure spray bars for applications such as coating, washing, cooling, moistening, lubricating, cleaning and disinfecting.
While spray bars are most commonly used with hydraulic nozzles, they can be used with all nozzle types including air actuated nozzles, air atomising nozzles and electric nozzles such as the EHP series.
.png?sfvrsn=8bfac992_1)
Why or when would you use a spray bar?
A spray bar will typically be used on a conveyor system that needs fluid to be applied to it in some way. This could be for cleaning the conveyor, moistening product on the convey or applying coating to something on the conveyor.
It is entirely possible to cover many conveyors with a single wide angle nozzle. So, if this is the case, why go to the expense of doing the same job with multiple nozzles in a spray bar?
There are multiple reasons why
1. Consistency of spray.
Most individual nozzles will not produce entirely even spray patterns; the edges of the spray will typically have less fluid delivered than the middle and, as suchn a multi nozzle spray bar is a way to deliver a more even spray across a target.
2. Improve impact
For cleaning applications we want to create impact from the fluid. A single nozzle would need to have a wide angle and be positioned quite far from the target so that the pattern can spread out enough. This dramatically reduces impact. A spray bar allows narrow angle, high impact nozzles to be positioned close to the target. This improves cleaning.
3. Desire gaps in target
In some conveyors we will have multiple product lines moving along. We might not want to spray in between these product lines as this would be wasteful. So we need a spray bar to position nozzles over each of the lines.
Spray bars for new processes or replacement bars
SNP will deliver your complete spray bar system. As well as designing new spray bars from scratch according to customer specifications, we also offer a swap-in service for customers that want to replace existing spray bars.
Because nozzles wear over time, impacting product quality, our spray bars are designed with future maintenance in mind. Whether a new bar or a swap-in replacement, we retain your design specifications, allowing you to request a complete replacement bar. This enables you to perform scheduled maintenance with minimal downtime and confidence in maintaining the intended spray performance. Our fabrication processes are compliant with requirements of food manufacture and other industries as we and our partners operate under ISO 9001 certification.
Precision spraying built on expert spray knowledge
839afdcb-269b-43a1-85f5-a70721aee594.png?sfvrsn=19e5c992_1)
Spray bars are actually quite simple things to make. At the end of the day, they consist of a piece of pipe with a few welded on threaded holders for the nozzles. This is not rocket science so any competent fabricator could make a spray bar. So, why buy from a specialist company like SNP?
Nozzle placement across a spray bar's horizontal axis is a design specification that requires careful consideration of the nozzle spray characteristics and the intended spray target. The number of nozzles and the spacing between them are key parameters that determine the precision and accuracy of the spray. A lack of proper consideration can lead to inefficient use of the spray liquid. In food industry applications, efficient spray bar design delivers:
- Achievement of ingredient tolerances
- Improved manufactured product quality
- Reduction of water consumption
- Sprayed ingredient cost reduction
When we design a spray bar for customers we use our expert knowledge of spray nozzles and work backwards from there. The final layout of the spray bar is fully determined by specialist knowledge of the individual spray patterns that need be generated to deliver the optimal spraying detailed above.
How nozzles will be laid out will depend on the knowledge of the application type, the fluid being sprayed and a whole host of other factors. This detailed knowledge of spraying is beyond the knowledge of most generalist steel fabricators. This is why it is better to buy a spray bar from a specialist spray nozzle supplier, who understand sprays and spray technology.
And, as you will see below, we take the hassle out of specifying your spray bars!
Quick and simple 3-step spray bar configuration
Currently, process engineers rely on multiple suppliers to deliver a functional spray bar. This adds significant project risk in the form of delays, spray bar quality issues, increased costs, and uncertainty regarding the accuracy and precision of the spray. Often, process and operational managers are left to deal with inefficiency costs post-installation. We make the configuration of your spray bar as easy as possible.
Step 1 We work with you to define your specifications. If you have an initial enquiry, why not start HERE.
Step 2 We finalise your design and send you a quote
Step 3 We deliver your finished spray bar in 4-5 weeks*
* Time estimates exclude delays from customer end
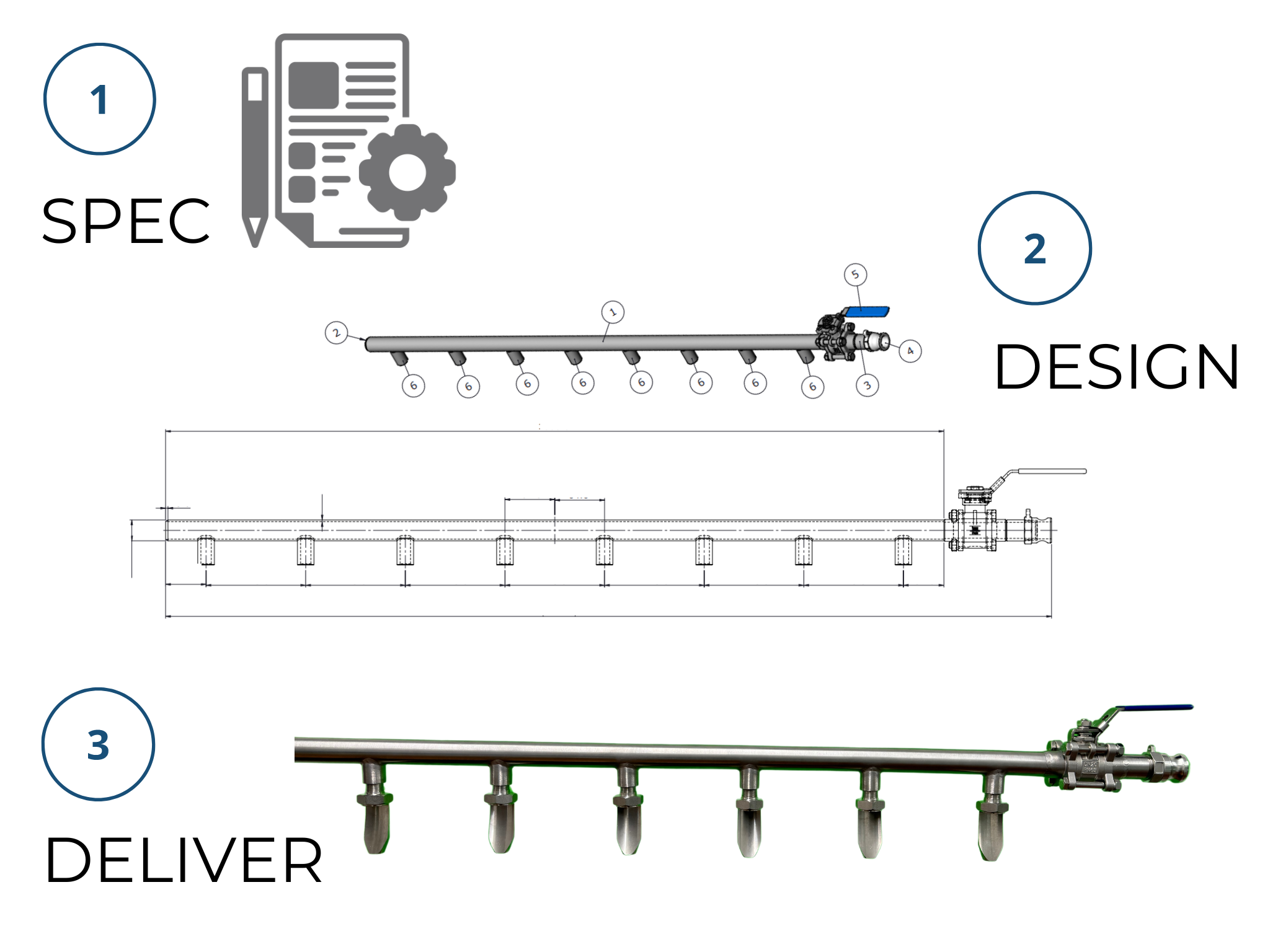
Why choose SNP for your one-stop shop spray bar system
SNP is your go-to partner for successful spray engineering. We apply our four decades of experience, expertise and technical knowledge in spray engineering to the design and production of spray bars. In line with our mission to deliver hassle reduction, optimise efficiencies and give our customers peace of mind, the benefits of using SNP to design your spray bar are:
Hassle reduction
Reduce design burden
Using our expertise, we transform your spray application needs and tailored nozzle selections and spray bar design
System integration
Our spray bars can adapt to your existing setup. Reducing the need to make changes to your setup
Fast turnaround time
We aim to deliver a complete spray bar in 4-5 weeks* from initial enquiry.
* Time estimates exclude delays from customer end
Improved efficiency
Product production cost
Our expertise enables us to design a full spray bar system that efficiently delivers the required amount of liquid to the target area. Enabling you control over production costs
Low downtime
Following initial order, we can supply an exact swap replacement for both spray bar and nozzles
Low maintenance
Our spray bar and nozzle systems do not require any special maintenance. They are designed specifically to enable low down time replacement ensuring low downtime
Efficient water consumption
Whether it's coating, washing, cooling our high-quality nozzles and expert teams help us enable our clients to successfully reduce water consumption
Peace of Mind
Improve process quality as well as food production quality
Remain within ingredient tolerances
Our primary focus is helping you achieve your spray goals. Employing our nozzle expertise to ensure you can achieve the desired spray quality and remain within process ingredient tolerances.
Standard compliant
We operate to ISO 9001 certification.
Reputable trusted suppliers
Our dedication to supplying customer needs over the years has earnt us trust in food manufacture and other vital industries.
If you have an initial enquiry, why not start
HERE.