Tangential whirl nozzles for spray injection
The required fluid whirl is created by the motion of the fluid through the nozzle prior to the exit from the orifice. In the case of tangential whirl the fluid initially flows at a right angle to the orifice and is twisted down before exit. This twisting motion is responsible for creating the whirl – hence "tangential whirl". A natural benefit of this configuration is that the full cone pattern can be achieved without the need for an internal swirl core giving greater clog resistance.
The design of this nozzle means the tangential profile is lower than other designs. If inserting a lance or injection quill into a pipe then this fact will allow for easier insertion and less cutting of the pipework.
The draw back of tangential whirl nozzles is that the will only produce a viable spray pattern above a certain flow rate. If lower volumes of fluid need to be added then it may not be possible to deploy this design of nozzle. Even the low flow variant tangential whirl nozzles have minimum flow rates above many spiral or impingement design nozzles.
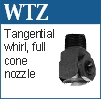
For other designs of
nozzles for injection please click here.