Rotary jet cleaners

Rotary
jet cleaners or impingement cleaners bring high powered cleaning jets to bear on each part of the tank. See below for our full range of these powerful cleaning heads.
Rotary jet CIP systems are at the forefront of tank cleaning technology
and offer measurable improvements in all key areas of the cleaning process.
The costs of ineffective cleaning
The cleaning of tanks and vessels is often an overlooked source of inefficiency and cost in the manufacturing process. Contamination through poor cleaning can result in the loss or recall of an entire batch of product. Having to carry out
secondary manual cleaning when CIP systems haven't done a good enough job means longer downtime and more water, caustics and heat usage. Even where a CIP system is doing a reasonable job of getting a tank clean, it may be taking longer
than it needs to or be using excessive amounts of cleaning products or water.
The cleaning mix
Any cleaning application has four components that contribute towards its effectiveness.
1- Time. The longer the cleaning is performed the greater the cleaning.
2- Chemicals. This is the dissolving effect of chemical cleaning fluids including
water.
3- Mechanical action. This is the physical action of the cleaning spray to dislodge residue.
4- Heat. Generally the hotter the cleaning fluid the better the cleaning action.
Increasing any of these 4 components will improve overall cleaning but there will be a cost associated with each. The cost of each of these elements will differ depending on the application and there may well be other constraints in place.
For example, in food processing applications there will be limits on the types of chemical that can be applied.
Understanding the differential cost of each element is the key to efficient cleaning. Optimising the mix of elements
is the process of increasing one element of the mix that has a lower cost (e.g. mechanical action) so that another element that has a higher cost (e.g. heat) can be reduced. The net cleaning power will remain the same but the cost associated
with the cleaning process will be reduced.
The relative contribution of each of the 4 elements of the cleaning mix can be represented on a Sinner Circle diagram as shown below.
In the left hand diagram, mechanical action is decreased perhaps by lowering pressure or by using an omnidirectional spray nozzle. This means that heat and time need to be increased to compensate.
In the right hand diagram, where mechanical
action is increased by increasing pressure or by changing from spray nozzles to jet cleaners, heat and time can be reduced.
Water efficiency
Water is not one of the 4 elements of the mix but water usage clearly is an important factor. The amount of water used in any cleaning mix depends mostly on the role of the chemical element and the time element. Water is known as the universal
solvent as it dissolves more substances than any other liquid. As such it often makes up all or the majority of the chemical component of the cleaning mix.
It should also be obvious how a reduction in the time component of the cleaning
mix will reduce water consumption. The shorter the cleaning cycle is the less water will be used.
Reducing water usage is a key driver for many businesses because it is an easy way to measure efficiency. Estimating the true
cost benefit of improved time or reductions in chemical action or heat can be difficult. The benefits are sometimes hard to measure and quantify. Water usage, however, is easy to measure. As we know that water consumption does
equate to the 'time' and 'chemical' element we can use it as a proximate measure of tank cleaning efficiency in many cases.
In the diagrams below, the use of a rotary jet cleaning system (the bottom diagram) increases the mechanical action
which greatly reduces water usage as well as time and caustic use.
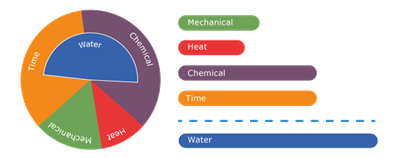
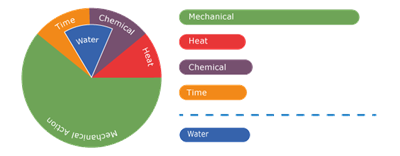
How do rotary jet cleaners work?
As the water jet hits the tank wall it explodes outwards dislodging residues by mechanical action. This use of mechanical force via a water jet is far more energy efficient than other methods of tank cleaning meaning that rotary jet cleaners are
the most water efficient tank cleaners available.
The jet cleaner will rotate on two axes and will have either 2, 4 or 8 (twin headed) cleaning jets. As these jets rotate they move through a set cleaning pattern that will, over a set period of time (the cleaning cycle) ensure that jets are
brought to bear on each part of the tank. This results in a very powerful and efficient clean for medium and large tanks.
Rotary jet cleaners are extremely easy to maintain - watch our disassembly and reassembly video here:
Uses
Jet cleaners are the most efficient way of cleaning medium and large sized tanks between 2 and 50 metres in diameter. And for tanks much above 6 metres in diameter they are normally the only viable option.
Also for very tough residues the jet cleaner will be the most water-efficient system as other cleaning systems will simply take too long to break down the residues. It is true that water and solvents will eventually remove all residues even in low
impact systems but it may take a long time. The mechanical force of a high impact jet exploding outwards from the point of impact is a far more energy efficient way of dislodging even stubborn residue.
Limitations
Rotary jet cleaners are normally only a sensible option for tanks with a diameter greater than 2 metres, although they can be deployed to clean particularly tough residues in smaller tanks.
Whilst rotary jet cleaners can be used at pressures as low as 3 bar they are most effective when powered by fluid at around 6-10 bar. As such, to get the most from these tank cleaners booster pumps that can get pressure to these levels will be required.
Rotary jet cleaners will typically require 125 mm openings to fit through and some of the larger models will need more than this.
Variations
We have a range of rotary jet cleaners, each of which has a variety of nozzle sizes and configurations.
Orbitor 2 is our range of 2-nozzle tank cleaners. The two nozzle design maximises the jet power but also means a
longer cleaning cycle.
Orbitor 4 is the 4-nozzle range of tank cleaners to give quicker cycle times and the option of 180o cleaning
Orbitor Dual - This variation has twin nozzle
heads with up to 8 nozzles in total. This can be configured to clean between 90o and the full 360o and has the quickest cleaning times.
Orbitor Compact - This model can fit into a 100mm opening
and, with the arms vertically aligned, will squeeze through an 8.5mm opening. The Compact is one of the few tank cleaners that is ATEX certified for use in all zones and temperatures.
Orbitor Eco - A fast cycle jet head that can complete a cleaning cycle in under two minutes.
StormBlasterTM - The Storm Blaster is a heavy duty range of tank cleaners suitable for cleaning very large tanks such as storm water attenuation tanks. It can be configured to clean between 170o and
360o and has a sealed gearbox meaning it can handle fluid with a high particle content.
D3000 and D4000 - These are heavy duty cleaners designed for large tanks such as marine crude oil tankers and are approved by Bureau Veritas