Water efficiency in dairy spray applications
The dairy industry has high water costs. This is due to high water usage and the relatively high cost of treating waste water. Cutting water costs is a key issue for many dairy producers. Selecting the correct spray nozzles and tank cleaners for the job can help achieve this goal. With tank cleaning in particular moving away from old spray ball technology and over to the more water efficient impingement cleaners will often have a dramatic reduction in water consumption.
Retro fit is easy
Fast Cycle jet cleaners have been designed to work at low pressures and flow rates meaning they can be retro fitted easily to existing CIP systems. Often there is no need to change the pump duty, pipework or openings. In many cases it is possible to simply swap out the existing inefficient spray balls for a jet cleaner and instantly reap the benefits of reduced cleaning time and water consumption per cycle. The improved power of the cleaning can also result in a dramatic reduction in caustic usage and/or heat. This simple process can supercharge a CIP system.
How it works
The 4 elements of cleaning
The overall 'cleaning' delivered by any tank washing system is made up or 4 key elements: mechanical action, heat, chemical action and time. Different cleaning heads have different relative makeups of these 4 elements. Water consumption is generally a function of chemical action and time, so cleaning heads that rely less on these elements will tend to be more water efficient.
The 4 elements can be illustrated on Sinner Circle diagrams as shown below. Each shows the relatives contribution to overall cleaning for each tank cleaning scenario.
What is the difference between Fast Cycle Jet Cleaners and standard jet cleaners?
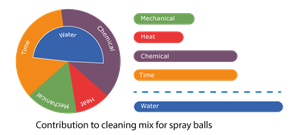
Both types of tank cleaner work on the same principles. They are both fluid powered, so the rotary motion necessary to bring the cleaning jets to bear on each part of the tank is provided by driving a turbine within the tank cleaner. The difference is in how the internal gearing is configured.
With traditional impingement cleaning the drive turbine is geared to rotate the jets quite slowly. This is to ensure the cleaning jets have sufficient dwell time on the tank surface to maximise impact. Further to this, a slow rotation speed delivers a longer overall effective jet length as there is little or no jet breakup due to the lateral motion of the jet as it sweeps the
tank. Conventional wisdom has meant that cleaning cycles of under 10 minutes were deemed too fast and would sacrifice too much cleaning power.
Fast Cycle jet cleaners throw conventional wisdom out of the window and approach cleaning from a different perspective. Rather than focusing on maximising cleaning power the FCJC looks at minimising water consumption. These new machines are geared to run very fast with cycle times as low as 1.7 minutes. These fast speeds do sacrifice some cleaning power and jet length. However, when compared to other types of tank cleaning nozzles they are far more efficient.
NOTE: Even though the fast cycle jet cleaners have less overall cleaning power the relative contribution of the mechanical action element of the cleaning mix is higher than in slow cycle jet cleaners. For more details please see the technical article linked here.
Enough is enough and too much is a waste
Many residues do not require high impact cleaning. Any impact over a certain critical point is, in effect, wasted energy and water. The reduction in the impact from FCJC's does not, therefore, translate to a reduction in effectiveness for many residues. The increased speed and massively reduced water consumption per cleaning cycle, however, does represent very significant efficiency gains over and above other types of tank cleaning head.
Spray balls vs fast cycle jet cleaners
-no-title.jpg?sfvrsn=72cefc92_0&MaxWidth=155&MaxHeight=&ScaleUp=false&Quality=High&Method=ResizeFitToAreaArguments&Signature=C3CC2046014283D47A4C9BD4CB038086)
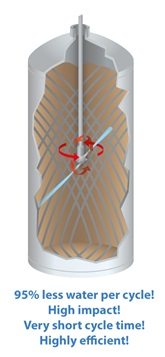
Fast Cycle jet cleaners are almost always more efficient than static spray balls. How much more efficient will depend mainly on how long the spray ball needs to be run to break down the residue in question. In most cases spray balls are only suitable for light or medium residues but even for these easier to clean tanks the spray ball may need to be run for some time to achieve a complete clean.
FCJC machines have similar or lower flow rates when compared to spray balls so a general rule of thumb is if the spray ball needs to be run for anything more than a few minutes then replacing it with a FCJC machine will save both time and water.
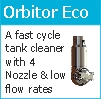

Up to 95% water saving
FCJC Vs Rotary Spray Balls
.jpg?sfvrsn=b5cefc92_0&MaxWidth=155&MaxHeight=&ScaleUp=false&Quality=High&Method=ResizeFitToAreaArguments&Signature=C2760BB93BFB9BC5A545E851DD7DDD06)
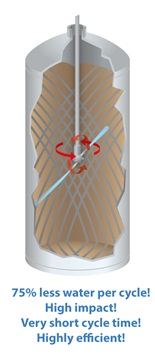
In many situations rotary spray balls will also be far less water efficient than the new FCJS machines. Whilst rotary spray balls do improve impact they still may take some time to break down a residue. They will typically have lower flow rates than FCJS machines but generally if a rotary spray ball is taking longer than 10 minutes to complete a cleaning cycle then an FCJS will be faster and more efficient.
Up to 75% water saving
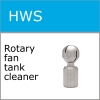
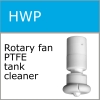
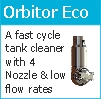
FCJC vs standard jet cleaners
Comparing FCJCs directly to standard impingement cleaners is problematic. Whilst the two machines operate in an identical way they actually serve quite different functions. A standard impingement cleaner is looking to leverage greater efficiency by increasing the contribution of the mechanical action component of the cleaning mix. A FCJC machine, on the other hand, is seeking to provide only a moderate and sufficient level of impact at fast speeds and low flow rates resulting in a very water efficient cleaning system. The long and the short of it is that standard cycle jet cleaners will be more efficient than FCJC cleaners if there is a tough residue or a large tank as the greater impact from their cleaning jets more than compensates for the increased cycle time. With lighter residues or medium sized tanks then FCJC will still provide sufficient impact to quickly clean with one pass and so the faster cycle times will result in a far more water-efficient clean.
Up to 33% water saving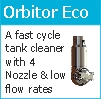
Where to use fast cycle jet cleaners?
Fast Cycle jet cleaners like the Orbitor Eco can be used all the main vessels used in dairy processing. Where it is fermentation tanks, pasturising tanks, storage silos, maturation tanks the powerful mechanical action of the machines jets will strip away tough residues using far less water than spray balls.