Precision spray nozzles - food processing
Precision spraying of small metered amounts of fluid is a common application within the food industry. There are two types of spray nozzle that allow for precison spraying - air atomising and electrically actuated.
Electric Nozzles
The Electric HydroPulse nozzle has an integrated solenoid valve to rapidly regulate the on-off cycle of the nozzle. / The solenoid valve is positioned inside the nozzle so that it is very close to the orifice. This means the reaction time of the shut-off system is incredibly fast. The nozzle can be cycled on and off up to 150 times per second.
In addition to the electrically modulated spray nozzles, SNP can also supply the hardware and software for controlling the nozzles. The FlexFlow control panel is an off-the-shelf box built for precision spray control. Furthermore, we can design and build all the necessary spray manifolds to position the nozzles correctly. When combined the EHP nozzles, the FlexFlow control panel and the spray manifolds represent a complete, precision spraying system.
Variable flows (pulse width modulation)
With such fast and reactive on/off cycle times the Electric Hydropulse can vary the flow from the nozzle without varying the fluid pressure. This is achieved by pulsing the nozzle very rapidly, (pulse width modulation - PWM). So, for example, a half flow could be achieved by having a 0.05 second on to 0.05 second off cycle time. This would halve the overall flow rate at any given pressure. Because the on/off cycle is so fast the resulting spray remains very evenly distributed even when targeting fast-moving conveyors.
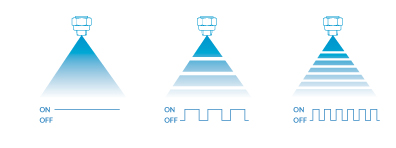
With a normal hydraulic nozzle flow rates could only be controlled by varying the fluid pressure. This, however, will alter other important spray characteristics such as droplet size. When variable flow rates are required due to, say, different product lines, it might not be possible to achieve the required variance with a hydraulic nozzle. This would mean a nozzle change between production runs. The Elctric HydroPulse will mean the same nozzles can be used despite variable dosing requirements.
Air atomising nozzles
The XA series of air atomising nozzles allow for exactly this. As a twin fluid nozzle, the breaking up of the spray into a fine pattern is achieved by smashing compressed air (or other gas) into the primary fluid. The use of air in this way gives a number of advantages for food processing applications.
1- Very low flow rates of fluid at low pressures can be finely atomised. If the pressure of the fluid itself was used to break up the flow (as in other types of nozzle) this would not be possible.
2- The XA series of nozzles can be fitted with an automatic shut-off needle that is powered by the compressed air system. This allows for precise 'stop/start' spraying, for example on a moving conveyor of product.
3- The level of atomisation can be varied independent of fluid pressure.
The XA series comes in a number of configurations. Full details on the whole product family can be found by clicking on the box below.
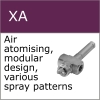
For yet further control still the SAM series of air atomising nozzles could be considered. These nozzles have a secondary air feed that is used to control the shape of spray. This means that both levels of atomisation and spray pattern can be varied by changing air pressure independent of each other and of the fluid pressure.
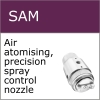