Dosing for coating applications
Accurate dosing is critical in coating applications. If too much coating is applied then money is being wasted and product quality may suffer. If too little is applied then product quality will almost certainly suffer resulting in rejected batches. Dosing is particularly challenging when the process line is fast moving. Any small changes in spray consistency can dramatically increase or decrease the coating being applied.
Controlling dosing for conveyor based systems
Dosing on a conveyor system can be controlled in two ways :
Conveyor speed
Simply by speeding up or slowing down the rate at which the product moves under the spray bar will increase or decrease the level of coating applied. Conveyor speed has the advantage of being completely independent of the spray/fluid properties so is often the easiest way to control dosing.
Flow rate
The flow rate through a nozzle can be increased by either using bigger orifice nozzles or by increasing the pressure at which the fluid is sprayed. Both options will also affect the consistency of the spray. Larger nozzles will tend to produce sprays with bigger droplet sizes whereas a flow increase induced by higher pressure will produce a spray with smaller droplets. As droplet size can affect the coating quality, care needs to be taken when controlling dosing through flow rate.
With air atomising nozzles that have external air mix configurations (the atomising air is mixed externally with the fluid) the flow rate through the nozzle is independent of the air pressure. So flow can be controlled by fluid pressure alone. What this means is that any changes in droplet size caused by an increase in fluid pressure/flow can be compensated for by varying the atomising air flow/pressure. However, it should be noted that in standard air atomisers this can vary the shape of the pattern unless a nozzle with an independent spray shaping air flow is used.
Nozzles such as the SAM have independent air inlets for spray shape, atomisation and nozzle actuation. In this way droplet size and spray shape can be controlled independently of flow rate.
Pulse width modulation
With electrically actuated nozzles dosing can be controlled via pulse width modulation. These nozzles can be cycled on and off up to 150 times per second. This means that if very rapid pulsing of on/off cycles is programmed the nozzles will deliver less fluid but, because the cycle is so rapid, there will be no noticeable difference in the continuity of the spray. So, a continual even coating will still be delivered. By using this technique, the same nozzles spraying at the same fluid pressure can deliver variable flow rates. As the fluid pressure remains the same, other spray characteristics, such as droplet size, remain constant.
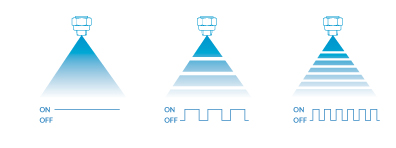
Controlling dosing for drum and fluidised bed coating systems
Dosing is controlled by the level of contact with the granules/capsules being coated. This can be controlled to some extent by the time of the process but, due to the randomised motion of the product within the spray zone, it is possible that some product may be over coated while other product may still require more. More time will, of course, develop the coating on the undercoated products but this will result in some product having too thick a coating.
In order to produce a more even coating one needs to ensure that all the granules develop a coating at roughly the same rate, meaning they all end up with an acceptable coating at the end of the process. Achieving this requires a complex balance between droplet size, spray pattern and the speed at which the drum rotates / the conditions of the fluidised bed. SAM nozzles have independent air inlets for atomisation (droplet size), spray pattern shape and on/off activation, making them ideal for these complex scenarios.