Gas cooling nozzles
The cooling of gas flows by injecting water or other coolants is a very common application for our spray nozzles. Correct nozzle selection is of critical importance in many spray cooling applications as the properties of the spray will determine how quickly heat is absorbed and where the spray will reach within a given gas flow.
Nozzle selection
When spraying into a hot gas flow above the boiling point of the coolant most of the cooling is caused by taking heat from the gas to evaporate the fluid. The rate of evaporation will depend on the average droplet size of the spray. Sprays consisting of smaller droplets will evaporate far more rapidly than sprays containing larger droplets. In fast moving gas flows this can be very important as often cooling needs to be achieved before the gas reaches another point in the process. Correct nozzle selection can thus reduce the need for long quench chambers.
Not just droplet size
Whilst sprays consisting of very small droplets will absorb heat faster they will also become entrained within gas flows more easily. This means that if a spray is too fine it may only cool a channel within a gas flow rather than the whole gas volume. So there is often a balancing act to be performed between getting sufficiently small droplets to achieve rapid heat transfer and having enough larger droplets to carry the spray into a gas stream and distribute it evenly.
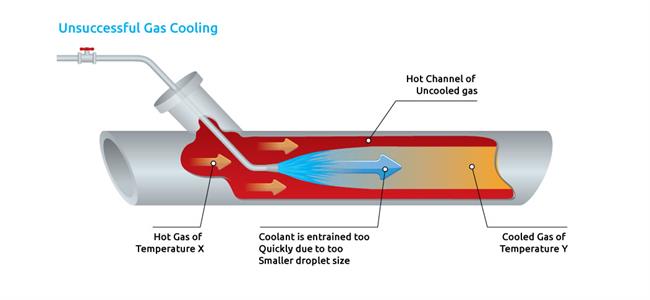
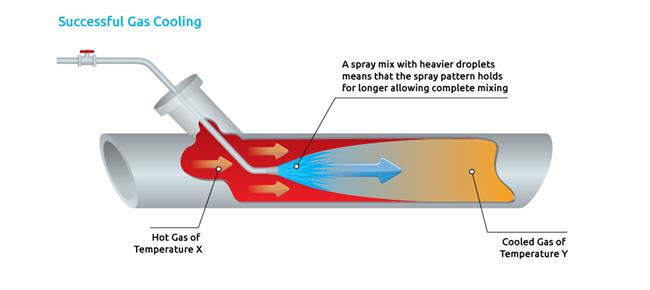
Variable gas flows
In many applications the amount of gas that needs to be cooled can vary depending on operating conditions. For example the pre-quenching of hot flue gasses before they enter a scrubber may vary dramatically depending on what is happening further up the process line to produce the gases. Variable cooling loads present problems for spray cooling because lowering the amount of coolant spray will typically mean lowering fluid pressure which will increase the droplet size and thus increase evaporation time. This means that in lower gas flow scenarios cooling may not be achieved in time, or may necessitate the need for a deliberately larger quench chamber.
There are a number of ways in which good nozzle selection can help overcome variable gas flow cooling problems. The use of spillback nozzle systems means that droplet size can be kept relatively steady even if the pressure and flow rate are reduced. Alternatively air atomising systems with variable air and fluid pressures can be used to maintain smaller droplets at reduced flows. Finally multi nozzle arrays can be deployed to give variable flows at stable droplet sizes.
Spray nozzles
Gas cooling nozzle selection will vary greatly depending on the application. For many cooling applications our spiral TF nozzles produce an excellent combination of small droplets mixed with some larger droplets to give penetration into rapidly moving gasses. For variable gas flows our spillback lances can provide optimum cooling even under highly changeable process loads. Our spriral air (SA) nozzles give a robust air atomising system suitable for use in hot gas flows that require finely atomised sprays for rapid quenching.
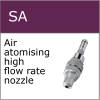
As gas cooling is a wide and highly varied application other nozzle types may well be recommended depending on the situation.