Full cone nozzles - Spiral design
The spray pattern is formed by impacting the fluid onto a protruding helix after exit form the spray orifice. The liquid then shears off the helix, breaking into droplets and forming the spray pattern. The spirals actually produce concentric rings of multiple hollow cone spray patterns with a less uniform liquid distribution between the cones to produce an approximate full cone pattern. By varying the geometry of the helix, however, a hollow cone pattern can be achieved.
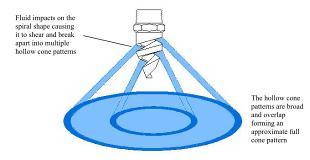
Spiral nozzles will, for any given flow rate and pressure, produce a full cone spray with the smallest droplet size for any direct pressure nozzles.
Spiral nozzle fluid distribution pattern
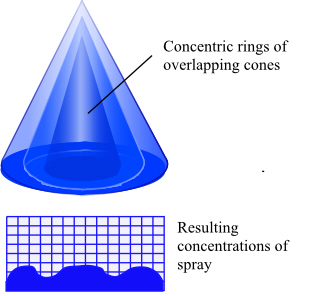
Spiral nozzles do not produce as even a coverage as other designs of full cone
nozzle because, as discussed, the full cone pattern is actually made up from
several overlapping hollow cones of spray. Whilst this feature may mean they are unsuitable for some applications it is actually an advantage in others. The concentrations of heavier droplets in rings has the effect of pulling the lighter droplets along with the spray. So spiral nozzles can be used to deliver fine droplets to areas where they simply would not reach with a standard whirl type nozzle. This is particularly important in
firefighting applications as it allows the spray to deliver fine droplets through strong thermal air currents increasing the overall cooling power of the spray.